Coronavirus, l’ingegnere italiano che sfida le multinazionali per salvare la vita ai pazienti con le sue valvole in stampa 3D
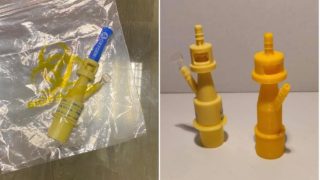
All'ospedale di Brescia scarseggiano le valvole di un macchinario che permette ai pazienti che lottano contro il Coronavirus in Rianimazione di ricevere ossigeno. Il fornitore non riesce a produrle in tempi brevi. Interviene l'ingegnere Cristian Fracassi che con una stampante in 3D in poche ore ha ridisegnato e stampato il pezzo mancante salvando la vita dei pazienti. L'intervista
La tecnologia d’avanguardia come quella della stampa in 3D può salvare vite, anche in situazioni di emergenza come quella del Coronavirus. E’ quello che è successo in un ospedale Brescia, uno dei nosocomi in prima linea nella lotta al Covid-19, dove stavano finendo le valvole di un respiratore, il macchinario che permette ai pazienti in Rianimazione di ricevere ossigeno. I medici lanciano l’allarme e cercano di mettersi subito in contatto con l’azienda che produce queste valvole. Ma il fornitore non può realizzarne in tempi brevi. La soluzione rapida è la stampa in 3D. Così con l’aiuto della direttrice del Giornale di Brescia, Nunzia Vallini, e del fisico Massimo Temporelli, i medici dell’Ospedale di Chiari contattano l’ingegnere bresciano Cristian Fracassi che con una stampante in 3D in poche ore ha ridisegnato e poi stampato la valvola mancante che serve a far funzionare il respiratore in Rianimazione per tenere in vita i pazienti che lottano contro il Coronavirus. TPI lo ha intervistato. Ci ha raccontato come può la tecnologia avanzata della stampa in 3D aiutare anche a salvare vite umane.
“Siamo andati fisicamente in ospedale e abbiamo preso le misure del pezzo. L’abbiamo ridisegnato in 3D. E l’abbiamo provato a stampare. L’ospedale ha preso il mio modello, ha fatto dei test preliminari per capire se era sterilizzabile e ha provato ad agganciare uno al respiratore e dice che funziona”, racconta a TPI l’ingegnere Fracassi.
“I medici lo stanno utilizzando. Al momento funziona, lo stanno tenendo monitorato per vedere se l’ossigeno viene mescolato in maniera corretta con l’aria. Però per il momento è in funzione. Non so quanto dureranno queste valvole ma nel frattempo ne stiamo realizzando altre 100 perché è questo il numero di cui ha bisogno l’ospedale. E con piacere andrò a portargliele. Nel frattempo io e il mio team stiamo realizzando altri tre modelli di valvole per fare dei test e per capire se sono riutilizzabili più volte. Stiamo cercando di capire se la sterilizzazione danneggia la valvola stampata in 3D o se rimane in vita. Nel frattempo comunque ne sto stampando un centinaio per portarle all’ospedale”, ci spiega.
“Sì, l’azienda produttrice della valvola potrebbe denunciarmi per plagio, perché di fatto è stato copiato e replicato il loro pezzo. Ho copiato un pezzo. Ho dei legali che stanno valutando la questione, non me ne sto occupando io personalmente perché preferisco dedicarmi a questo. Poi se sarà sbagliato o giusto non sono io a deciderlo, spero nessuno. Spero che la cosa si risolva qua e basta. In ogni caso sto portando avanti le mani perché in un mondo in cui i soldi contano più della salute di qualcuno non si può fare altro. E’ una multinazionale quella che stiamo toccando ad ogni modo, non si tratta quindi di un’azienda piccola. Ha sede a Lussemburgo, quindi non ha interessi con l’Italia di nessun tipo”.
Assolutamente no.
“Io dico che non stiamo violando nulla, per il semplice fatto che siamo in una situazione di emergenza. In una condizione standard tradizionale un’ospedale dice ‘compro una macchina non voglio comprare la valvola e quindi me la autoproduco per praticità perché me la regalano’. Ecco quella sarebbe una violazione. In caso di emergenza in teoria si potrebbe – credo, così mi riferiscono – saltare alcuni passaggi. E’ un filo sottile, non sono un legale”.
“Sì, non mi era mai capitato prima. Io tra l’altro ho anche un’azienda farmaceutica quindi in qualche modo conosco gli iter burocratici. Tra una settimana ho un’ispezione per un altro prodotto che sto aspettando da un anno”.
“No, è un cerotto. Però appunto conosco l’iter per ottenere una certificazione, ci vuole oltre un anno. E’ impensabile dire ‘faccio lo stampo e attendo la certificazione un anno’. Nel frattempo muoiono delle persone. Qui è una questione di ore. In un iter standard servirebbero mesi, delle volte anche anni”.
“Sì, sono tutte plastiche. In realtà stiamo stampando con tre tipi di stampanti diverse, alcune a filamento altre a resina e altre a polvere. Non so ancora quale di questi pezzi funzioni meglio. O se funzionano tutti e tre o nessuno dei tre. Il primo modello che abbiamo realizzato è a filamento. Perché è quello che ci permette di realizzare nel minor tempo possibile”.
“A filamento 2 ore e mezza per ogni valvola, per quella a polvere invece ci vogliono circa 40 ore e a resina 24 ore”.
“Esatto”.
“E’ un respiratore. Quindi chi non è in grado di respirare in maniera autonoma e che viene intubato gli viene messa una maschera nella quale viene inserito ossigeno in una determinata quantità che stabilisce il medico”.
“Ne servono molte, per ogni paziente va cambiata”.
“Penso di sì, non so se solo la valvola o tutta la maschera. Comunque questo componente è scarso. Ai pazienti ricoverati manca”.
“Sì, viene già utilizzata in ambito odontoiatrico soprattutto. Adesso sarà mia premura contattare le persone che possono avere prodotti più o meno idonei o comunque più vicini all’ambito biomedicale. Per il mio momento ho utilizzato polimero biocompatibile e addirittura commestibile perché il dna è derivante dal mais quindi è una bioplastica sostanzialmente. In ogni caso non è un pezzo che va finire dentro lo stomaco o anche solo in bocca. E’ solo un collegamento tra un tubo e una macchina per “banalizzarlo””.
“Se ci fosse richiesta in larga scala su tutta Italia l’azienda mi taglierebbe la testa perché sarebbe come rovinargli il mercato. L’azienda l’ho contattata più volte ma loro si negano anche se mi piacerebbe risolvere con loro la faccenda e non scavalcarli”.
Perché visto il successo non viene utilizzata la stampa 3D?
“Perché non è per nulla semplice. Quando ho visto la valvola ho visto la complessità, ha tanti passaggi dei canali dove passa l’aria che hanno un diametro inferiore al millimetro. La stampa in 3D non ha una grande precisione non arriva alla stampa di 0,8 millimetri. E quindi li stiamo realizzando addirittura manualmente. Dopo la stampa vengono comunque controllati fisicamente uno ad uno a occhio per controllare che i canali siano tutti passanti”.
“Una volta che ho in mano la valvola originale, con il calibro mi vado a misurare tutte le geometrie me le disegno in 3d con il pc e una volta che ho il disegno me lo salvo in un formato idoneo per la stampante e lo dò in pasto alla stampante che mi realizza il pezzo. “.
“Sto adottando dei provvedimenti. Sto toccando il prodotto con guanti e appena è stampato lo metto in una busta sterile anche per il trasporto. Cercando di contaminare il prodotto il meno possibile”.
“Di almeno un centinaio”.
“Certo, ma hanno detto piuttosto che niente testiamolo”.
“Che con la stampante in 3D in meno di 24 ore un potenziale problema è stato risolto, nel senso che avevano una necessità, serviva una valvola speciale, è stata disegnata e realizzata e testata e al momento funziona. Non è sicuramente l’iter preferito, sono consapevole che non sia la strada migliore. Se ti si rompe il laccio di una scarpa o la cerniera di una porta o una maniglia si può utilizzare senza problemi. In ambito sanitario e medico dove ci sono rischi di morte è proprio l’ultima spiaggia da utilizzare. E dato che questi medici erano alla frutta e all’ultima spiaggia abbiamo deciso di utilizzare la stampante in 3D. E’ la più veloce. E forse in questo caso serve la velocità e non il resto”.
“Sì in altri Paesi il suo utilizzo è ormai sdognato. Ci sono stampanti in 3D che stampano case. Se ne parla ancora poco in Italia. Anche nel settore nautico qualche mese fa hanno stampato un’intera barca in meno di 24 ore. Il vantaggio elevato della stampante in 3D è quello di avere un prodotto in pochissimo tempo”.
“No, in Lombardia faccio l’80 per cento del mio fatturato. Sono molto territoriale. Abbiamo un territorio aziendale molto denso a livello europeo che è quello di Brescia”.
“La stampa 3D ha dei vantaggi e degli svantaggi grandi. Il vantaggio grande è appunto la velocità di realizzazione del componente. Lo svantaggio è nella precisione e nella durata del pezzo piuttosto che nella resistenza del pezzo. Un pezzo stampato in plastica con la stampante 3D resiste molto meno di un pezzo in plastica stampato con i metodi tradizionali ad iniezione ad esempio. Se volessi stampare il classico bicchiere dell’acqua in plastica usa e getta che ha uno spessore inferiore al millimetro. Con la stante in 3d farebbe acqua da tutte le parti. Con gli spessori così sottili per esempio di un bicchiere usa e getta in plastica non lo riesco a realizzare. Mi servirebbe solo come modello. Per vedere la forma. Non da utilizzare per bere. Nulla vieta che con il tempo prenda sempre più piede. Come ha preso nel settore plastico e adesso anche in quello in metallo perché la prossima rivoluzione è quella delle stampanti in 3d in metallo”.